Design-build approach proved superior in water treatment project
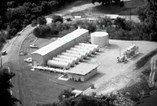
Western Region Environmental Vice President and Principal,
Sverdrup Civil, Inc., Costa Mesa, California, USA
And Joanna Madenburg
Western Region Marketing Project Manager
Sverdrup Civil, Inc., Costa Mesa, California, USA
Contents
Pressure filtration used for first time in California
Numerous technical, design, and material innovations used
Design-build approach helped mitigate typical obstacles
Single source of accountability streamlined management
Keeping pace with the new millennium, the focus of integrating design and construction services as part of the innovative design-build process is a benchmark method in project delivery. This approach for the Casitas (CA) Municipal Water District responds to an evolving marketplace that demands capabilities of building higher, faster, and stronger.
The project, including all pilot testing and approvals, was finished 19 months from the contract award in March 1995, helping CMWD meet its deadline to have the plant significantly completed by June 1996. Using new technology, innovative design, and fast-track construction to meet regulatory requirements with a minimum financial burden, the project was completed at US$9.3 million.
Local lake provides drinking and irrigation water
Providing a safe water source for Ventura County, California, USA, and an irrigation source for the 2,300 ha of citrus and avocado orchards, the CMWD's new Marion Walker Pressure Filtration Plant sends approximately 25 x 106 m3 of water from Lake Casitas to the area's 65,000 customers. Constructed in 1959 to provide long-term drought relief, the original reclamation system collected and stored water from the undeveloped 370-km2 Ventura River watershed in Lake Casitas. Original project facilities included a nine-gate, multi-level intake structure at the face of Casitas Dam, a dual chlorination disinfection process, and a 210-km pipeline distribution system.
Fire damage, taste and odor episodes, poor quality rainfall runoff causing lake turbidity, and the need to meet federal mandates led the CMWD to examine methods for providing the community with a safe, cost-efficient, and effective program for water treatment.
Pressure filtration used for first time in California
Blending the skills of scientists and engineers with the expertise of design and construction specialists, the CMWD implemented a technology that had never been proven in the water industry in California. The result was one of the first high-capacity (2.8 m3/s) water treatment plants to successfully use pressure filtration to meet the California Surface Water Treatment Rule (CSWTR).
The project's process design and smooth construction proved the merit of using an alternative process, which had primarily been used in the oil industry. Large pressure filtration systems with in-line coagulation were successful in filtering and distributing oil sources for years. Based on this proven success in complex industrial applications, it was a logical transfer from oil to water.
New process removes 98% of particles greater than two microns
Pressure filtration typically guarantees more than 98% removal of all particles greater than two microns. Using pressure filtration allowed the CMWD to maintain the hydrostatic head behind Casitas Dam, which facilitated the downstream pumping system without the application of additional pumping.
Significant electrical energy savings were realized with the application of pressure filtration. The primary challenge to applying pressure filtration in CMWD's case was to maintain water quality parameters with the instantaneous flow changes that are caused by large downstream pumping demands, while avoiding the use of clearwell storage. A pilot test would prove it.
Pilot test demonstrated ability and soundness of process
To demonstrate that pressure filtration could meet regulations for filtering drinking water, a pilot test demonstrating the validity and soundness of this approach was required by the California Department of Health Services. Because the project was under a tight 19-month schedule to meet the regulatory mandate deadline, plant design and testing had to occur simultaneously.
The pilot test, a scaled-down version of the pressure filtration system, was run with various flow rates and several chemical mixtures to assure efficient operation under diverse conditions. All 10 pilot tests were completed, confirming the overall design criteria for the 2.8 m3/s (64 million gallons per day) plant. Compliance was established with the DHS turbidity goal of less than 0.2 NTU at loading rates of up to 8.1 x 10-3 m3/s per m2.
Numerous technical, design, and material innovations used
As part of the high-pressure filtration capabilities of the plant, the system has numerous technical, design, and material innovations. In its 2.5 years of operation, these applications have provided substantial energy cost savings, environmental damage mitigation, accurate filtration rates, less administrative and maintenance personnel requirements, and overall operation cost savings. These benefits have been achieved through:
- The backwash and rinse recovery systems were key to elimination of discharge in natural streams. Liquid process discharges from the plant were prohibited due to the lack of a sewer system in the area and sensitive creek habitat. Because of these strict requirements, the plant was designed to recycle 100% of filter to waste volumes from backwashes, eliminating discharge to the natural streams through a rinse recovery system based on use of the natural hydraulic gradient behind Casitas Dam.
- A fully automated Supervisory Control and Data Acquisition (SCADA) system anticipates, diagnoses, paces, and schedules the plant and distribution operations. The system has the ability to control flow variable magnitudes. Efficiency was maximized by linking all sites via a radio frequency (RF) process control network—minimizing initial installation and life-cycle costs while providing communication performance in an easy-to-maintain system. The system's components include process control of the new pressure filtration plant, remote site connectivity to the 160 km2 district (including the central plant and office locations), intelligent pumping schedule control based on demand, and automation of the new and existing chlorination processes. Most importantly, the system's data works to track filtration performance.
- Turbidity meters and particle counters work to verify the treatment process, assuring that the filtered water product meets all regulatory requirements. These electronic sampling systems test before and after filtration to verify that the water distributed to system users is free of contaminates and meets all levels of safety for drinking water.
Process uses filtration to remove turbidity, Giardia, and virus-sized particles
Providing the community with a safe and efficient means of drinking water as well as an irrigation source, the pressure filtration system treats water from Lake Casitas by chlorinating, cleaning, storing, and distributing the product throughout northern Ventura County. The process uses filtration to remove turbidity, Giardia, and virus-sized particles to acceptable levels. The system was designed to assure at least partial treatment operation at all times through a redundancy of various system components. Also, no process wastewater is discharged at this site. Dried sludge is periodically removed from the drying beds and hauled off to a landfill site. Four main components direct the system's functions:
- Chemical Feed Systems. Through a pump system, chemicals are added to a constant raw water bypass flow of 3 x 10-2 m3/s. The flow is taken from the 1400 mm pressurized raw water pipe and boosted in pressure before the chemicals are added. The treated stream is then re-injected into the main pipe approximately 6m downstream through a sparger to assure thorough mixing of the chemicals at all flow conditions. Both chemical feed pumps are flow-paced from a total plant flow signal.
- Filtration. Working to separate the chemically treated water source from the solids, the filtration plant simultaneously functions as an air release and a vacuum for the water source. Treated water is distributed to Casitas customers via a pipeline distribution system after passing through anthracite and garnet filter media, while the solid coagulant is moved on through the backwash stage. This is done using eight 3.6m-wide by 15m-long horizontal steel pressure vessels with motor operated butterfly valves for influent, backwash water supply, backwash water discharge, drain down, rinse/filter to waste, and air scour supply control for the backwash cycle. A hydraulically operated valve modulates filter effluent flow. The filtration process design is based on equal flow through all filters in service so it assures high filter flow will not exceed system capacity.
- Backwash. Once the product water has passed through the filter, this two-step backwash sequence pushes air through allows the water to settle, and applies a three-minute backwash flow to remove particles. This sequence is repeated, concluding with a final rinse with filtered water in the down flow mode. To assure that the final rinse water is not combined with the backwash water, two dedicated rinse water pumps take suction from the filter effluent side and boost the pressure to recycle the rinse water back to the head of the plant.
- Backwash Wastewater Reclaim System. The backwash water is reclaimed and put through a Lamella clarifier and pressure filter before being reintroduced to the raw plant influent. Four process water pumps collect waste streams and forward them into the backwash water surge tank for treatment in the reclaim system. The surge tank, with a 625 m3-capacity, is continuously turned over by two mix pumps to prevent settling of solids from the filter backwash. The wash water is transferred to two separate clarifiers that operate in parallel. Booster pumps feed two vertical pressure filters continuously blending the filter effluent with treated raw water, forwarding the product to the main filter plant. Integrated sludge thickeners installed below the settling portion of the clarifiers further increase the solids content. Sludge is periodically pumped to one compartment of three sludge drying beds. Further dewatering occurs when excess water filters through a sand layer in the drying beds. It is collected through drain piping and transferred to a pump where it is recycled back to the backwash surge tank.
Design-build approach helped mitigate typical obstacles
The design-build (D-B) approach implemented helped to mitigate many of the unforeseen challenges that can occur on typical D-B projects. These challenges can include schedule delays and budget overruns caused by problems such as ineffective construction staging, unnecessary project change orders, miscommunication with multiple responsibility parties, and additional administrative steps such as bidding. By implementing the project through the D-B approach, many design and construction challenges were avoided because of only one responsible party. The CMWD ended up with a project completed within the 19-month schedule duration and US$20 million under the original estimate.
The D-B approach, compared to the traditional approach of retaining a design engineer and then selecting a separate construction contractor, has many advantages. D-B guarantees project cost at the preliminary design stage; provides a single-source responsible for the entire project, simplifying communication and coordination; and it promotes fast-track scheduling, shortening project duration by overlapping design and construction schedules. Since the facility is delivered faster, cash flow begins sooner.
Even as designers were finalizing details on the plant, equipment orders were placed and construction workers were on site, leveling the construction site and establishing building locations. This helped control construction costs by keeping the schedule moving on a fast-tracked basis. Site work, underground utilities, and concrete were conducted while final design drawings were being finished. All major equipment and pipe were also pre-purchased. This saved many months off the project schedule.
Using the design-build process saved $20 million
Using the D-B process and overlapping the design and construction schedules saved the CMWD over US$20 million from their original estimate. CMWD Board President Bill Austin thinks highly of the D-B process, noting, "Sverdrup has done a great job ... they provided us with a single source of financial accountability which gave us peace of mind."
The D-B approach, emphasizing single-source management, commitment of the client, and buy-in of the community, has played a key role in overcoming the difficulties encountered on this project. Its successful outcome was based on key application efforts, including:
- Cost-effective delivery without interrupting existing plant operations. As the communities still needed a water source during construction of the new pressure filtration plant, existing plant operations were maintained throughout the D-B process. Construction of the new system included the addition of two pipeline connections to the existing 1400-mm distribution pipeline. These new connections used temporary blind flanges to keep water from flowing through the new plant's systems while construction was taking place during nighttime construction to keep impacts to existing operations low.
- Minimized disruption to surrounding communities. The public was brought into the D-B process through a partnership with the project participants. Public meetings kept the community informed of project activities. During the pre-construction stages, the public was asked about their project concerns. These concerns included construction traffic, noise disruption, dust control, and environmental disturbances. Evaluating these issues and developing strategies early helped minimize or avoid community impacts.
- Successful pilot testing. The pilot test proved that the system shutdown required for tie-ins from new plant to the existing pipeline could be completed in only 22 hours, when the original time frame was 48 hours. This tie-in was planned in detail and the residents were individually informed of the possible 48-hour outage ahead of time. This resulted in zero complaints from residents for the shutdown switchover and proved the project would be completed by the 1996 regulatory deadline.
By September 1996, the plant was running on an eight-hour-a-day basis while project challenges were worked out. The issues encountered during the start-up phase dealt with changes to process control, focusing on accommodating the system demands and the interrelationships of process components. By December 1996 the system provided continuous treatment of the entire Lake Casitas water source with concurrent performance testing of the plant systems. Testing determined successful performance, which met all established requirements.
During the first year of operations at the Marion R. Walker Pressure Filtration Plant, the system continuously met and exceeded the requirements of the SWTR and the performance goals set by the DHS.
Single source of accountability streamlined management
With a single source of accountability under the D-B process, the CMWD streamlined budget and project management, reducing their administrative costs. Key to the project's success were efforts including:
- Partnering between the design-build team and the CMWD. All project participants were involved in formal partnering to encourage open communications and common goals. The successful partnering effort has been lauded by the CMWD. According to the agency's Principal Engineer, Steve Wickstrum, "On this design-build project, everybody has worked together in a real team approach. Working with Sverdrup has been a very positive experience for the whole staff and the board at CMWD."
- Extensive community involvement efforts. The project team's mission was positive and ongoing community interaction with full disclosure to educate the public about the legitimate need for the project. The public was included in the project development process through public meeting forums, a public involvement program established by a community relations committee, and communications through Preserve Our Parks, a local environmental organization. Through these mediums, the community's interests were tracked and monitored, assuring that all stakeholder needs were met. Community events provided more involvement, including the Groundbreaking Ceremony, Fishing/Barbecue Day, and the Ribbon Cutting Ceremony. Community support was strong as all the project's construction subcontractors and many of the suppliers were Ventura County residents. Business revenues were kept local and the community saw a surge in the local economy as a result.
- Preserving the environment. Surrounded by state parks and recreation areas, the Lake Casitas environment is a pure and natural setting. Preserving the condition of the lake and the surrounding areas was a top priority for all project participants. As part of the project approach, an environmental mitigation plan was developed and implemented, resulting in several environmental preservation measures. The treatment plant system was designed to recycle 100% of wastewater backwash, eliminating contaminated discharge into the area's natural streams, and trees were preserved and the wildlife habitat protected. An alternative plant design was developed to allow for the plant facilities to blend into the natural environment. The site design resulted in a much smaller "footprint" than a conventional treatment plant. This resulted in fewer disturbances to the natural environment and decreased visual impact.
- Operating efficiency. Because the system is controlled through a SCADA system, the utility and operation costs of managing water pressure, flow, direction, location, and system maintenance are lower. The SCADA system is easy to maintain—one individual can control the entire operation. The program can monitor and control the entire system, or can focus on an area as small as an individual pump. Thirty-three remote sites comprised of pumping plants, chlorination stations, reservoirs, and monitoring stations communicate via RF, with anticipated monthly savings of US$3,000 compared to the more traditional approach of a leased telephone line configuration.
The project, including all pilot testing and approvals, was finished 19 months from the contract award in March 1995, helping CMWD meet their regulatory deadline to have the plant significantly completed by June 1996. Using pressure filtration technology (new to water systems), D-B methods, and partnering with all project stakeholders, the project met all regulatory requirements. The project was completed on schedule and under budget at US$9.3 million, saving CMWD US$20 million over their original estimate for a conventional water treatment plant.
Bibliographic References
Dettmer, A.; Lange, P., P.E.; Wickstrum, S., P.E. (June 1997). Meeting the Surface Water Treatment Rule Turbidity Goals with Inline High Rate Pressure Filtration at Lake Casitas, California. American Water Works Association (AWWA) Annual Conference and Exposition.
Olsen, D.; Rao, T., P.E.; Wickstrum, S., P.E. (June 1997). Partnership: The Cornerstone of a Successful Community Participation Program. American Water Works Association (AWWA) Annual Conference and Exposition.
Rao, T., P.E.; Wickstrum, S., P.E. (June 1997). Taking Advantage of Regulatory Updates in California. American Water Works Association (AWWA) Annual Conference and Exposition.
Sverdrup Civil, Inc. (1996). Casitas Municipal Water District Pressure Filtration Water Treatment Plant. Western Council of Construction Consumers Distinguished Project Awards Program.
Sverdrup Civil, Inc. (1998). Marion R. Walker Pressure Filtration Water Treatment Plant. Orange County Engineering Council National Engineers Week Award.
Wickstrum, S., P.E.; Johnson, J. (April 1998). Casitas Municipal Water District, Marion R. Walker Pressure Filtration Plant, Summary Report and Evaluation for the First Year of Operation. Submitted to California State Department of Health Services.
Author Biography
Roy C. Fedotoff, P.E., DEE, Western Region Environmental Vice President and Principal for Sverdrup Civil, Inc., has 28 years diversified experience including the overall planning, design, and construction management of water, wastewater, and water reclamation projects. He has written and/or presented over 45 papers on environmental engineering
Joanna R. Madenburg, as a Sverdrup Civil, Inc. Western Region Marketing Project Manager, plays an integral role in directing the company's environmental business development efforts. She routinely manages technical papers, develops proposals, and directs presentations for a variety of Sverdrup water, wastewater and water reclamation projects.
For more information, contact Sverdrup Civil, Inc. at 925-256-7500 or e-mail: fedotorc@sverdrup.com.
Information is from a paper presented at the 1999 International Congress on Local Government Engineering and Public Works held recently in Sydney, Australia.
Edited by Joyce Jungclaus