French companies promote their solid-waste-treatment technologies
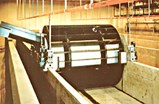
The interest in France to develop acceptable methods to deal with domestic waste is part of a much larger commitment throughout the European Community to come to grips with problems generated by waste disposal.
Stringent "green" laws are imposing innovative value-added pollution-control and waste-disposal solutions. The result in France has been the creation of sludge composting methods, accelerated fermentation techniques, thermolysis, and other technologies that can serve its needs and those of other countries.
Composting offers the low-cost, effective, and safe stabilization of waste. The treatment is suitable for sludge produced at urban wastewater plants as well as waste produced in households, which has been segregated from recoverable materials such as glass, metals, paper, and plastics.
Composting is most effective for waste with high organic content (peelings, dish water, etc.). Developing countries, where household waste has a largely organic content, are following French developments in composting with interest.
Accelerated fermentation composts raw household wastes
The French engineering company SGE Environnement near Paris has developed effective techniques of accelerated fermentation for composting raw household waste. Two to three weeks are sufficient to obtain compost of excellent quality suitable for agricultural use, instead of the several months of more traditional methods.

in Prairieland, MN, from an accelerated fermentation
developed by SGE Environnement.
SGE Environnement has constructed several dozen composting plants in France. It has also just completed one in Turkey, near Smyrna, and two others are under construction in Portugal.
These plants have a treatment capacity of 25,000 to 60,000 metric tons of household waste per year and cost around $10 million to build. They function by combining a BRS accelerated fermentation reactor with a Siloda composting area--both processes being exclusive to SGE Environnement.
The BRS reactor receiving the raw household waste is a rotating cylinder. Turning at a rate of half a turn per minute, it achieves total fermentation in two to four days. The waste then is deposited in composting rows in the Siloda area, which consists of parallel rows separated by low concrete walls. A wheeled shovel running on the separating walls traverses each row,
The wheeled shovel transfers the waste from one row to the other every two to four days in order to turn and fully aerate it. In the ground below each row a forced ventilation duct helps to aerate the heaps. The final compost is ready after six to eight transfers from one row to the other.
The Siloda process requires little space and helps contain bad odors. It also is suitable for sludge from water treatment plants and sorted refuse from household waste.
Thermolysis supplants incineration?
The French engineering company Thide Environnement SA, based in the Paris suburb of Corbeil-Essonnes, is keen on thermolysis.*
Thermolysis can treat raw household waste as well as MRF dregs, which mainly comprise organic material having a high calorific value.
The Thide system generates a combustible gas by "baking" the refuse in the thermolyzer--at a temperature sufficient to gasify the solid organics in an oxygen-deficient atmosphere. Thide has tested its kiln-type thermolyzer for several thousand hours.
The carbonaceous residue, called char, is processed for metal recovery and then fed to the melting furnace.
The French engineering company, in looking to promote its device to process raw household waste as well as municipal solid waste that has been sorted for its organic material, recently concluded a licensing agreement with Hitachi.
The Japanese company has since modified the Thide design.
The Hitachi kiln-type thermolysis system is designed to:
- 1. Reduce the thermolyzer to about one-half the conventional length and stabilize operation, by incorporating an independent drier.
2. Enable the thermolyzer to generate combustible gas that contains almost no chlorine and is therefore noncorrosive, can be burned to heat the thermolyzer, and can be used to generate high-temperature, high-pressure (500ÂșC, 100 atm) superheated steam for efficient power generation.
3. Permit recovery and recycling of unoxidized metals from the thermolyzer.
4. Be used as a vertical cyclone melting furnace that achieves a slagging rate of around 90%, minimizes carryovers, reduces dioxin generation, and uses a low-temperature-activated catalyst to hold the dioxin content of the exhaust gas to less than 0.01ng-TEQ/Nm3.
Hitachi has built a pilot plant in a region about 100 miles to the north of Tokyo. The company has been gathering and analyzing data from the plant and expects its analysis to be completed during 1999.
Thide Environnement believes the plant to be one of the first applications of thermolysis for the treatment of household waste.
For more information, contact the French Technology Press Office at 312-222-1237.