Orlando Utilities steered by business, driven by technology
Running a growing multiple-service utility as a business, with continued investment in technology, keeps the Orlando Utilities Commission on the road to serving its customers in a competitive and effective manner. OUC's business-focused and technology-driven operations have kept this utility a leader for more than half a century. It has used technology to maximize efficiency in all of its service areas, and with a renewed focus on business practices, OUC continues its competitive direction.
Center has made use of advancing technology
The OUC Water Production (WP) control center has a history of utilizing new technology, due, in part, to the diverse nature of the water resource upon which it relies. Water from the quarter-mile deep Floridan Aquifer is pumped to the surface through 31 deep wells, then to one of eight nearby water treatment plants for treatment and distribution.
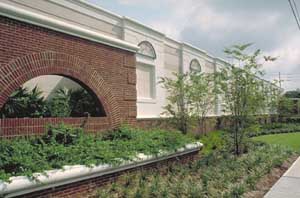
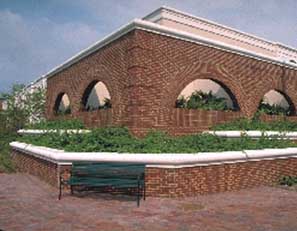
This utility produces an average of 93 million gallons per day (mgd) for the roughly 365,000 people who live in the City of Orlando and portions of Orange County. Because of the siting of the wells, treatment facilities are scattered throughout the nearly 200-square-mile area, a situation that led to the utility becoming an early user of remote operations. The distribution system comprises nearly 1,500 miles of mains. As early as the 1940s, a treatment system operator at a central site could manually operate equipment at the remote storage facilities. In the 70s, computerized communications systems were introduced to collect operating information as well, as start and stop pumps.
During the 80s, the first completely computerized supervisory and data acquisition (SCADA) system was installed with remote terminal units (RTUs) at each facility. The early 90s brought the need and opportunity to upgrade to the next generation of computers and open systems. "So we set in motion an upgrade project and, at the same time, considered what we should do from a strategic perspective," said WP Director Howard Smith recalling decisions that had to be made.
Technology upgrade anticipates new millennium
Continuing quality and growth issues precipitated "Water Project 2000," the utility's most comprehensive program in half a century to upgrade, improve, and expand the water system and its technology.
"Bob Haven came in as OUC's new General Manager and developed the concept for Water Project 2000," Smith said. "The comprehensive project, which was promised to our customers for delivery by the Millennium, allowed us to close five aging plants, build three new ones, and expand and improve four others. The project included conversion to a new treatment technology, replacement of existing automation and information management systems, and completion of distribution system improvements."
One of OUC's technological advancements was to implement an ozone treatment process to improve water quality. A new Facility Automation and Information Management (FAIM) system replaced the SCADA system, and a Facility Information Management (FIM) program organizes every detail of every piece of equipment and operation. A Historical Data System provides reports needed by staff throughout the utility.
Haven commented on how plants operated by companies that privatize utilities are run efficiently through the application of technology. He said, "We want to run our plants with one laptop computer. We're big on technology, utilizing it to reduce our labor and other operational costs."
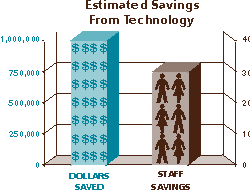
"The entire staff of the Water Production Division consists of 35 full-time employees working in operations, maintenance, and administration," Smith added. "Without the use of this technology, that number would easily be 60 or 65. In the past, new technology just meant saving money; now, new technology also means new benefits and opportunities."
OUC is a technology user and innovator
Since the Commission's deep water supply is protected from contaminants, pollutants, and bacteria that would affect surface water supplies, chlorine and fluoride injection have provided sufficient treatment over the years to achieve a safe product for delivery. The only remaining problem was the level of hydrogen sulfide in the water. While not harmful, the taste and odor of this gaseous compound often is equated to rotten eggs, as those of us in the business know.
For many years, OUC used the traditional treatment—aeration—to remove the hydrogen sulfide. While that helped improve the taste, it was unpleasant to neighborhoods around treatment facilities. "Some people thought they were living next to a plant treating sewage instead of their drinking water," Smith recalled.
Realizing this would be an ongoing problem, OUC worked with design consultant CH2M Hill to convert its treatment process to use an appropriate up-to-date system. As a result, the utility chose ozone as the disinfecting reagent now in use to eliminate compounds that tend to cause undesirable tastes and odors in the water.
A primary process objective is to bring all of the water pumped from the wells into contact with the gaseous ozone as quickly as possible. The ozone reacts with the hydrogen sulfide before decaying back into oxygen. Since OUC installed its ozone generation equipment, the new treatment process has:
- Minimized the use of chlorine
- Improved water odor and taste
- Enabled OUC to accommodate changes in water quality and meet or exceed future regulations
- Enabled OUC to house water plants in more attractive, low-profile facilities
- Eliminated the unpleasant odor associated with the aeration treatment
Some said FAIM wouldn't work
Not only is using the ozone treatment process primarily for hydrogen sulfide removal innovative, OUC has again pushed technology by remotely controlling it with its new FAIM system. According to Smith, "some said couldn't be done." He commented at this point how EMA Services, Inc., an information technology and management consulting firm headquartered in St. Paul, MN, was instrumental in the implementation of the FAIM system, especially with setting up programmable logic controllers (PLCs) and developing the historical data collection and reporting system.
FAIM is a state-of-the-art, fully automated control system featuring a distributed open architecture. Windows-based operator workstations and programmable logic controllers (PLCs) are integrated with OUC's information systems. A high-speed communications network uses fiber optics, frame relay, and T1 telecommunications services, as well as a 900MHz multiple-address system and spread spectrum radio, assuring communications under virtually any circumstances.
The FAIM system allows a single operator to monitor and control the entire system from the WP control center or from any other treatment facility. FAIM also controls the ozone treatment process for each facility.
"While it is very difficult to estimate the actual savings generated from automation and remote monitoring, I would say that we would have to spend an additional $1,000,000 or more per year in labor costs alone," if the plants were fully staffed, Smith estimated.
FIM system is a catalog of data
With the strong emphasis on remote, automated operation, proper and timely maintenance became even more critical because fewer people are available on staff to respond and operate equipment in the event of failure.
To capture, organize, and share the vast amount of knowledge and information needed to maintain the utility's facilities and equipment, WP developed its Facility Information Management (FIM) system. This is an "active catalog" of information relating to every aspect of operations and maintenance (O&M). Information about every motor, valve, pump, procedure, process, etc., eventually will be available through the system.
The browser-based interface makes FIM intuitive and easy for anyone to use. Clicking on a motor, for example, gives details about the parts involved, repair processes, and maintenance requirements. With an intranet access, changes or additions are immediately available to all members of the staff.
"Technology's value comes from the availability of complete and current information—when and where it is needed," Smith asserted. "FIM is a critical part of the new technology because it manages the information needed to link maintenance and operations, and to efficiently support unattended operations."
Historical data system keeps records up-to-date
The WP Control Center also is using intranet/browser technology to collect, maintain, and provide access to historical data collected from FAIM and from each facility. Regulatory and operating reports are available via browser, both within the WP and throughout the utility.
As access is user-based, data can be entered, modified, or retrieved at any computer in the OUC network. Template-based reports and forms are updated automatically to reflect data previously entered and schedules that change daily; modifications can be made without additional programming.
Technology's human aspect is key
Even in an environment that has always supported technology and encouraged change, any transition to the use of the latest technology can still be daunting. As Smith put it: "Some people have difficulty in a changing environment. People need a reason to buy into a new process. Give them a reason. People want to identify with a cause—if they have a reason, they'll have the right attitude." He added that as a supervisor he has to give his employees a cause to help foster a team spirit.
Although the major technology improvements coming into being as a result of Water Project 2000 will have raised consumer costs 10% a year for five years, the Orlando utility's delivered water is still less expensive than that of most other utilities in the area. How does OUC keep competitive without requiring more drastic price increases?
Business-driven thinking is encouraged
General Manager Haven sees the "big (business) picture" in every aspect of the multiple utility. Electric, gas, and water each provide unique opportunities for his entrepreneurial mind. He explained: "I believe in strategic thinking rather than strategic planning. We focus on new ideas, to encourage people with creative thoughts, and increase our ability to respond quickly to customers and their needs."
For example, customers can pay their utility bill at numerous locations, and by next year they'll be able to pay online with credit cards. OUC has developed a system to notify customers automatically by phone if there is a problem with their service.
Haven believes that meeting customers' needs sometimes means having to rely on instincts and watching what other utilities are doing. Despite the business focus that is key at OUC, "not everything needs to be cost justified," he said. For example, the conversion to ozone increased costs, but there has been product improvement as a result. He believes OUC has "one of the best systems anywhere. Our treatment process will handle any regulations in the future. We could increase production by 50% and still cover the demand."
Focus should be on opportunity
"Electric deregulation really got a lot of utilities into the ‘business mode,' looking for new revenue sources," Haven explained. "You need to focus on your core business and see what other opportunities exist within that scope. You have to be looking continually for opportunities to take initiatives."
OUC continually explores new opportunities, with several ventures underway or planned.
- Chilled water to cool downtown office buildings: OUC's chilled water service is a completely new revenue source. The utility can produce it more cheaply since it's produced along with water and electricity. Customers get an economical package price if they buy multiple services.
- Wholesaling to, or managing services for, other utilities: OUC can provide services such as call center staffing, laboratory services, or remote monitoring.
- Renting out currently unused warehouse space.
- Vehicle service and maintenance: The utility began some time ago to sell gasoline to the City of Orlando for police cars, and now it's maintaining the police department's fleet. This maximized one of OUC's under-performing assets.
- Mining biogas from a local landfill and using it to fuel one of the electric plants.
What lies ahead for OUC?
"We're looking at other options to grow the business and bring in new revenue sources," Haven explained. "But it's not only looking at new services, we're always looking at how to market more effectively what we already offer." So, what do Smith and Haven see in the future as OUC continues on its successful path?
Deregulation of water will not occur in the same manner as we've seen with gas and electricity, according to Smith. He believes "It will come in the forms of privatization, consolidation of services, and regional approaches to becoming more cost competitive. But the fundamentals will always remain the same; you need good business practices with the best technology you can get—they go hand in hand."
Haven concluded by saying that if an organization has good people and good plans, it will accomplish whatever it sets out to do. He said OUC has some of the best of both of these, "So we'll keep on planning and innovating."
About the Author: Paul Borzo is communications editor for EMA, Inc. of St. Paul, MN. This article appeared in the Fall 1999 issue of EMA's quarterly publication Communicator, and has been modified to conform to our online style.
Edited by Ian Lisk, Editor Emeritus, Public Works Online